Carbery Milk Products have just successfully completed a £1.9 million refit and expansion of the Cheese Chilling Plant at their Irish head quarters.
NH3 Refrigeration Ltd were pleased to be part of this expansion and refit by supplying the “One Day” chill Tunnel and associated Conveying Systems. The project entailed installing a new conveying system from both the Cheddar and Mozzarella lines, and integrating them into the new single “One Day” Chill Tunnel and onto a relocated robotic palletiser to achieve the maximum 236,000kg / day production.
To maintain the cheese quality, it is essential to have rapid cooling of the cheese blocks to +11°C in less than 24 hours. It was in 1970 that the tower block forming and high process temperatures forced cheese companies to make use of our rapid chilling tunnel. The quality issues without the rapid chill become so significant that the NZDB has always paid a premium for 24 hour cooled cheese blocks. Both the American and European industries are now seriously addressing the issue.
A “One Day” Cheese Cooling Tunnel improves product consistency and quality by reducing deformation. This in turn allows for improved cheese processing and automation. Bulk stacked blocks need up to two weeks for appropriate cooling. When thousands of blocks are produced per day, the required space is significant. The Cheese Tunnel is a relatively high density cooler requiring space for only one day’s production.
The Tunnel is always full of product. Simultaneous loading and unloading ensures that all shelves are constantly fully loaded. This makes it possible to achieve consistent air velocities over all of the cartons and all of the blocks can only be exposed to identical cooling conditions. The Cooling Tunnel is a “highly developed, extremely simple machine”. The simplicity of the FIFO operation results in fewer moving parts, reduced maintenance, reduced down time, simple operator interface, guaranteed consistent chilling results and lower capital cost.
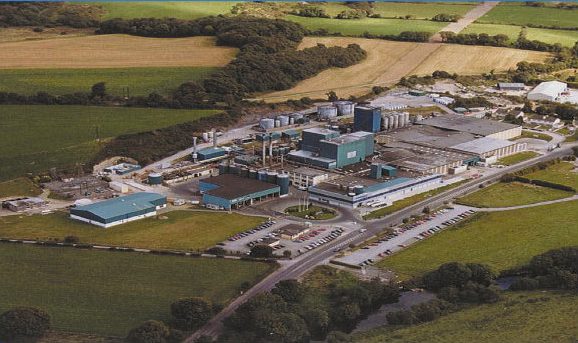